回想・・長い文書ですが是非お読みください。
また10月16日が来ます・・・17年前のその日、忘れもしない悪夢の始まり・・・後にも先にも、自分の勤める会社が無くなると思い足が震えたのはこの時が初めてでした。
金属異物が混入し、全国規模での製品回収・・・大規模製品回収事故の悲惨さを経験して初めて解りました。
その中から沢山のことを学びました。
リスクマネジメントの限界、HACCPの弱点、組織の冷淡さ、事故発生部署担当者の苦悩・・事故を起こしてもなお自社製品を支持してくれ、早期の復活を祈ってくれるお客様の多さ等々・・・
ただ一番辛かったのは、入社以来、仲の良かった先輩上司が責任を一身に背負い、自死してしまったことです・・・亡くなる前夜最後まで一緒に事故処理を行い、様子がおかしい事に気付きながら、トップマネジメントに伝える機会を逸して、救うことの出来なかった事への後悔・・・
事故は多くの人々の人生を狂わす魔物です。
また経験する必要のない出来事です。
でも、万一不幸にも遭遇したら・・・嵐は必ず去っていきます。
辛く苦しい事ばかりですが、その時まで諦めずに、悲観し過ぎずに、真摯に受け止め乗り切って下さい。
HACCPを導入すると食品製造時の安全性は向上する・・・それは神話です。
HACCPを正しく理解して、正しい方法で導入して、正しく運用管理を行うことが出来て初めて「HACCPは食品安全に寄与する」ことが出来ます。
今の現実は「ccpはこれね!」で、多くのHACCPシステムが構築されているのではないでしょうか・・・・
上に書いた事故を起こした現場はHACCPシステムの運用管理に手を抜いていたのではなく、むしろ積極的に取り組んでいた現場です。
それなのに事故を起こしました・・・・それはHACCPを正しく理解できていなかった為です。
危害要因の抽出方法を誤っていた・・・というより使っていた方法が当時の標準的なもので、そのように教育されていた全てでした・・・
それはどの企業でも同じで、今もその状態は変わっていないかもしれません。
国内のHACCP教育はHACCPプランの作成に至る経過を教えるのに熱心ですが、HACCPシステムの弱点を伝えていません。
特に危害要因を如何に多く・正確に見つけ出す方法やCCP以外の多くの危害要因の扱いを指導していないのです。
これでは危害要因の見逃しと、危害要因の放置が起き、事故が発生するのです。
HACCPシステムを導入した安心感から余計油断もします。
多くの失敗から得られた経験でHACCPシステム構築を指導できる人材の確保と養成を行わないと、これから先もHACCPシステム構築済み工場で事故は発生するでしょう。
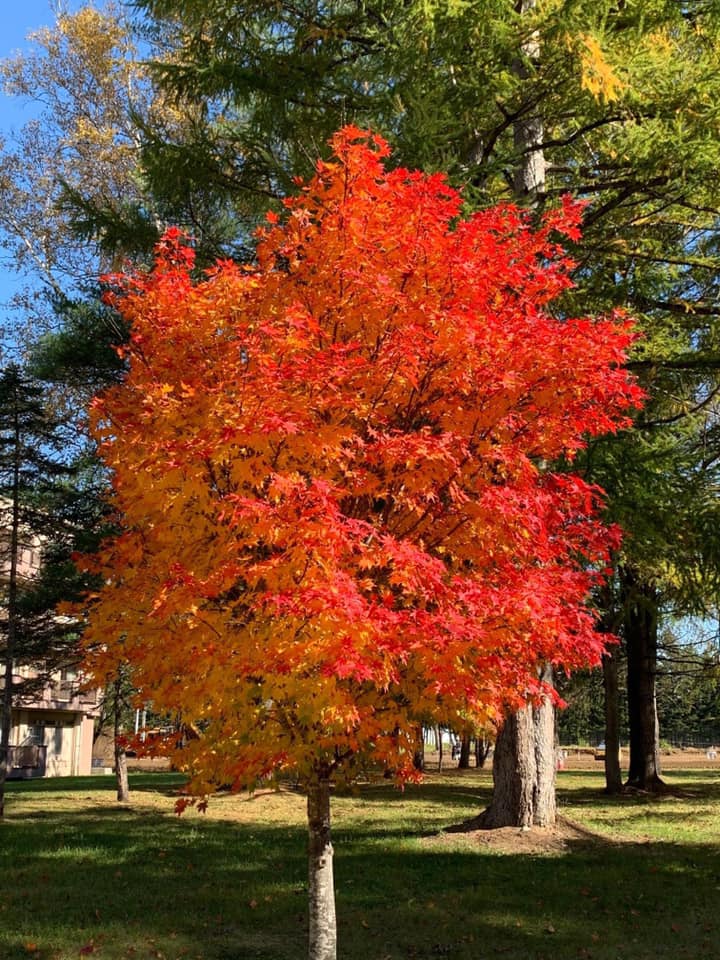